- Key Takeaways
- Understanding Die-Cut Design Fundamentals
- Required Tools and Software for Die-Cut Design
- Setting Up Your Document for Die-Cut Artwork
- Creating Die-Cut Artwork in Adobe Illustrator
- Working with Vector Shapes and Die Lines
- Mastering Layer Organization and Management
- Implementing Spot Colors for Die Lines
- Preparing Artwork for Production at namecards.com.sg
- FAQ
- What is die-cutting in printing?
- What are the different types of die-cut applications?
- What are the essential design considerations for die-cut artwork?
- What software is commonly used for creating die-cut artwork?
- How should I set up my document for die-cut artwork?
- How do I create custom die lines in Adobe Illustrator?
- How should I organize my die-cut artwork layers?
- How do I implement spot colors for die-cut lines?
- What should I do to prepare my artwork for production at namecards.com.sg?
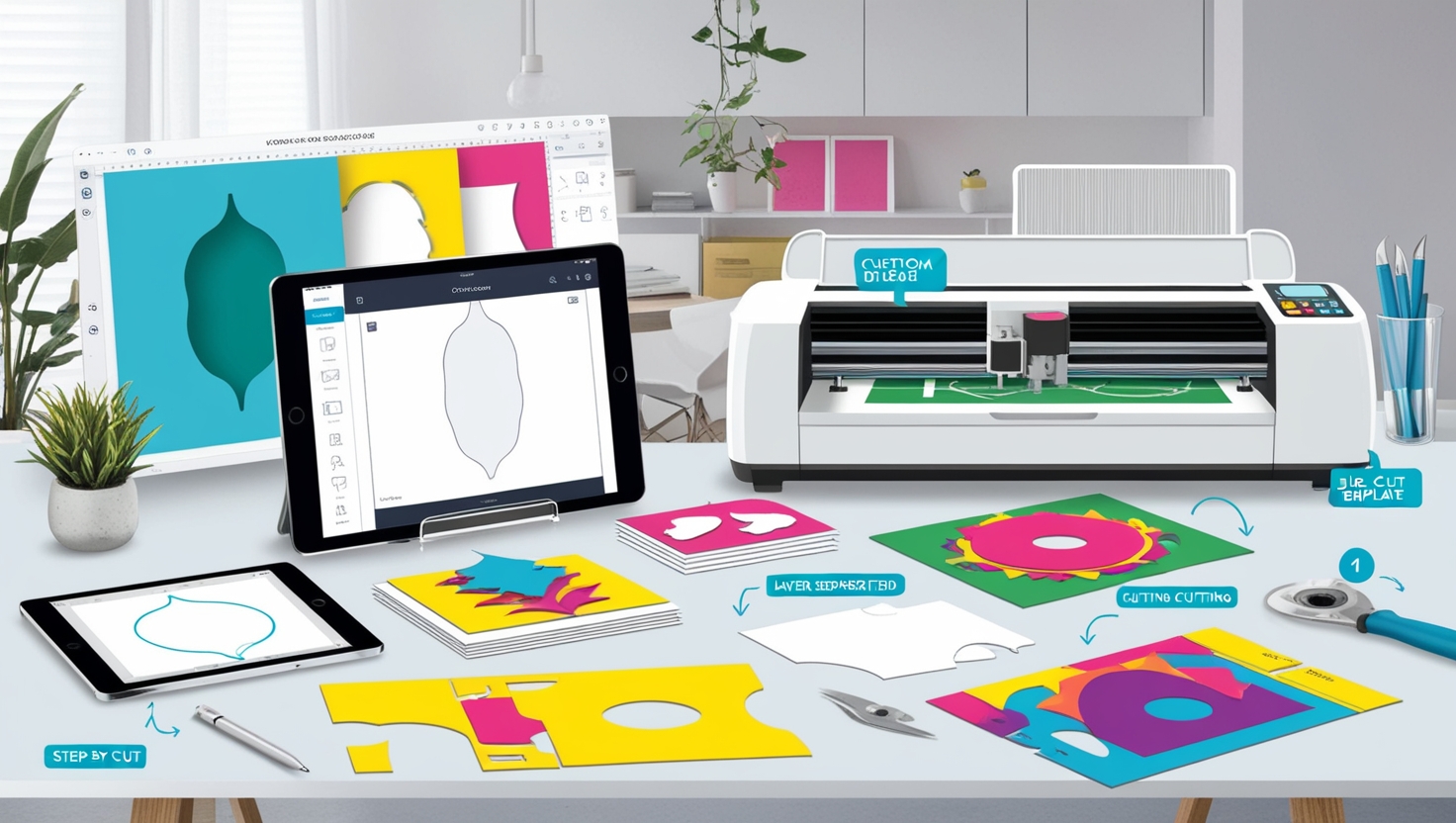
Die-cutting is a flexible printing method that lets you make detailed custom shapes and designs. It ranges from simple labels to complex packaging solutions. This guide will show you how to make die-cut artwork step by step. You’ll learn how to make your projects stand out with precision and visual appeal.
At the core of die-cutting is making a separate layer for die-cut lines. These lines are usually drawn in spot colors to make them stand out from the main design. By carefully preparing your artwork this way, you ensure a smooth transition from digital to physical print. This opens up a world of custom shapes and finishing techniques like embossing, debossing, and foil stamping.
In this guide, we’ll dive into the details of die-cut design. We’ll cover the basics and the technical aspects of file preparation and software use. Whether you’re an experienced designer or new to die-cutting, this step-by-step guide will give you the skills to enhance your projects with precision and flair.
Key Takeaways #
- Die-cutting lets you create detailed custom shapes and designs for various uses, from labels to packaging.
- Creating a separate layer for die-cut lines, using spot colors, and exporting files in PDF format are key steps in the die-cut design process.
- Thinking carefully about material thickness and finishing techniques like embossing, debossing, and foil stamping is important for the desired look.
- Learning the technical aspects of file preparation and software use is crucial for a smooth transition from digital design to physical print.
- Pay close attention to detail and follow a structured approach to create die-cut artwork that grabs attention and elevates your projects.
Understanding Die-Cut Design Fundamentals #
Die-cutting in printing is a versatile technique. It cuts stock materials like paper, cardboard, or plastic into specific shapes. A custom-made die is used for this. This method is key in packaging design and product branding, making products stand out.
What is Die-Cutting in Printing? #
Die-cutting is a special printing technique. It uses a steel rule die to cut materials into intricate shapes or patterns. It’s used for packaging, cards, brochures, and more, adding visual interest and dimension.
Types of Die-Cut Applications #
- Simple alterations: Cutting out holes, windows, or perforations to create unique openings and textures.
- Elaborate 3D-folded shapes: Designing complex, three-dimensional structures for book covers, children’s board books, and promotional materials.
- Packaging elements: Incorporating die-cut features into packaging design, such as handles, flaps, or custom shapes to enhance the overall aesthetic and functionality.
Essential Design Considerations #
- Separate layers for artwork and die lines: Ensure that the artwork and die-cut lines are on separate layers for better control and precision during the design process.
- Use vector graphics: Opt for vector-based designs to ensure clean, crisp edges and the ability to scale the artwork without losing quality.
- Implement proper bleed and safe zones: Allocate sufficient bleed area (at least 1/16″ beyond the die line) and maintain safe zones to avoid accidental white spaces or unintended cuts during the die-cutting process.
Understanding die-cutting basics and design considerations helps designers. They can make packaging, branding, and promotional materials that grab attention.
Die-Cutting Technique | Characteristics |
---|---|
Flatbed Die Cutting | Generally used for low-volume projects and larger-sized products. |
Semi-Rotary Die Cutting | Allows for quicker turnaround times due to the reduced number of times the material needs to run through the die-cutting system. |
Flexible Dies for Rotary/Semi-Rotary | Less expensive compared to solid dies, making them a cost-effective option for custom dies for labels. |
“Die-cutting is a crucial element in packaging design and product branding, enabling designers to create unique, eye-catching features that captivate the target audience.”
Required Tools and Software for Die-Cut Design #
To make amazing die-cut artwork, you need top-notch digital tools and software. Adobe Creative Cloud apps like Adobe Illustrator and InDesign are key. They give designers the power to make detailed die-cut templates with ease.
Adobe Illustrator is a must for die-cut design. It uses vector graphics, which stay sharp and clear, no matter the size. Learning to use vector graphics is vital for making custom shapes and precise designs.
But it’s not just about the software. You also need high-quality images, logos, and fonts to make your project pop. Choosing the right design elements can really make your die-cut designs stand out.
Tool/Software | Key Features |
---|---|
Adobe Illustrator | Precise vector-based design, custom die-cutting templates, path manipulation |
Adobe InDesign | Layout design, die-line integration, comprehensive print production capabilities |
Silhouette Software | Digital die-cutting, intricate shape creation, print-and-cut functionality |
With these tools and software, designers can really show off their skills. They can make die-cut designs that grab people’s attention and leave a lasting impression.
Setting Up Your Document for Die-Cut Artwork #
Creating die-cut artwork needs a well-set document for smooth printing. Here are the main points for setting up your document:
Document Size and Bleed Settings #
First, set your document size to the final trim size of your project. Add a 3mm bleed on all sides of your artwork. This prevents white edges or gaps after cutting.
Color Mode and Resolution Requirements #
Use CMYK color mode for print projects to get accurate colors. Your artwork should be at least 300 dpi at the print size. This ensures sharp, detailed prints.
Creating Essential Layers #
Organize your document with two key layers. One for the die line, labeled “Die” or “Die cut,” and another for your artwork, labeled “Art” or “Artwork.” This makes managing your design easier and reduces die-cutting mistakes.
Recommended Settings | Value |
---|---|
Bleed | 0.125″ (3 mm) on all sides |
Color Mode | CMYK |
Resolution | 300 dpi at actual print size |
Layers |
|
By following these guidelines for document setup, bleed settings, and CMYK mode, you’ll create top-notch die-cut artwork. It will wow your clients and engage your audience.
Creating Die-Cut Artwork in Adobe Illustrator #
Making amazing die-cut artwork in Adobe Illustrator is a big deal for designers and print fans. It’s all about creating cool vector graphics, Adobe Illustrator designs, and custom shapes. Learning how to die-cut is key for eye-catching print materials.
Start by using the Pen tool or Shape tools in Illustrator to make your die-cut path. Make sure the die line is right on the edge of the page but doesn’t touch it. This makes it easy to fit with your printed piece.
For detailed vector designs, use the ‘Unite’ function in Pathfinder to merge different parts into one shape. This is important for keeping your artwork solid and making die-cutting easier.
Then, use ‘Offset Path’ to add a safety zone around your design. This helps avoid any mistakes or damage during production. Make the die line colorless but change the outline to a bright spot color so it pops.
Finally, use ‘Simplify’ to smooth out any rough spots or corners. This gives your design a clean, polished look. By getting good at these steps in Adobe Illustrator, you’ll make top-notch die-cut custom shapes.
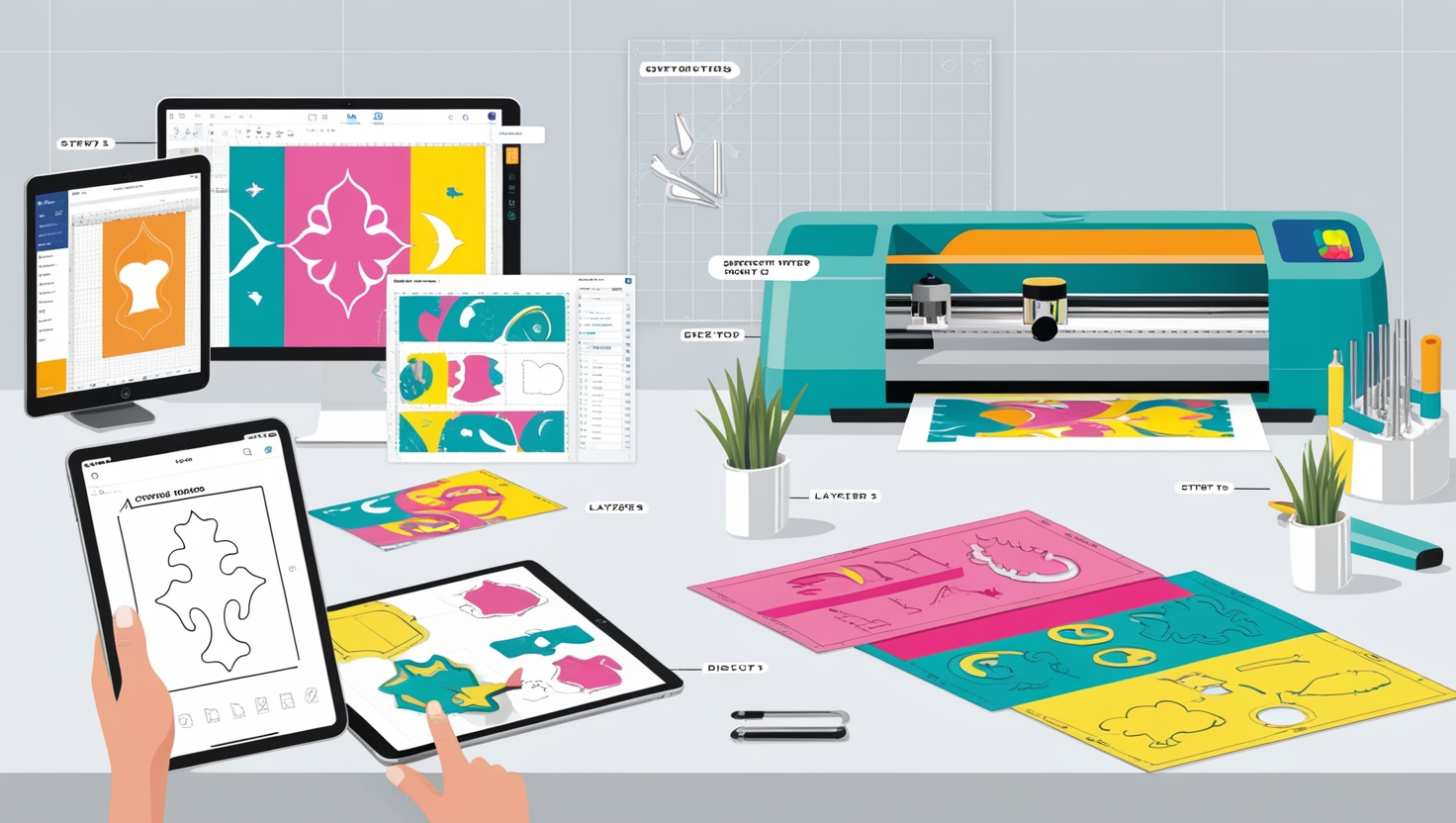
“The key to creating stunning die-cut artwork lies in your ability to seamlessly integrate the die line with your design, while maintaining the overall visual integrity of the piece.”
Working with Vector Shapes and Die Lines #
Mastering vector shapes and die lines is key for die-cut artwork. Vector shapes keep their quality and clarity, even when scaled up. Die lines are the blueprint for cutting, making sure the final product meets your vision.
Creating Custom Die Lines #
Making custom die lines in Adobe Illustrator is easy. Use the Pen tool or Shape tools to draw precise lines. Make sure all lines have the same thickness for a clean look. For fold lines, use dashed lines and a unique color to stand out.
Managing Path and Stroke Properties #
Details matter when working with die lines. Improve path and stroke properties for clean edges. Use the “Simplify” command or adjust points with the Pen tool. Also, keep a 3mm bleed outside the die lines to avoid white edges.
Implementing Safe Zones #
Safe zones are essential in die-cut design. Keep important design elements 1-2 mm from the edges. This ensures your design looks great, even with small production changes.
“Consultation with the printer/die cutter before finalizing the design is advisable to ensure feasibility and effectiveness of the die-cut artwork.”
By understanding vector shapes, die lines, and safe zones, you can make amazing die-cut designs. These designs will grab your audience’s attention and improve your brand’s look. Always work with your printing or die-cutting partners for a smooth production process.
Mastering Layer Organization and Management #
In the world of die-cut design, layer management and design organization are key. They can make or break your final product. By structuring your layers well, you can improve your workflow and print quality.
Start by organizing your design with separate layers for your artwork and die lines. This makes it easy to lock the die-cut layer. This prevents mistakes that could ruin your design. Make sure the die-cut layer is above your artwork but below other non-printing objects.
For complex designs, use sublayers for different parts of your artwork. This method improves layer management and makes editing easier.
Layer Management Techniques | Benefits |
---|---|
Separate layers for artwork and die lines | Prevents accidental changes, ensures proper hierarchy |
Use sublayers for different design elements | Improves design organization and editing efficiency |
Lock die-cut layer to prevent unintended edits | Maintains the integrity of the die-cut design |
Mastering these layer management techniques will make your die-cut design process smoother. Your artwork will be ready for printing, meeting all quality standards for success.
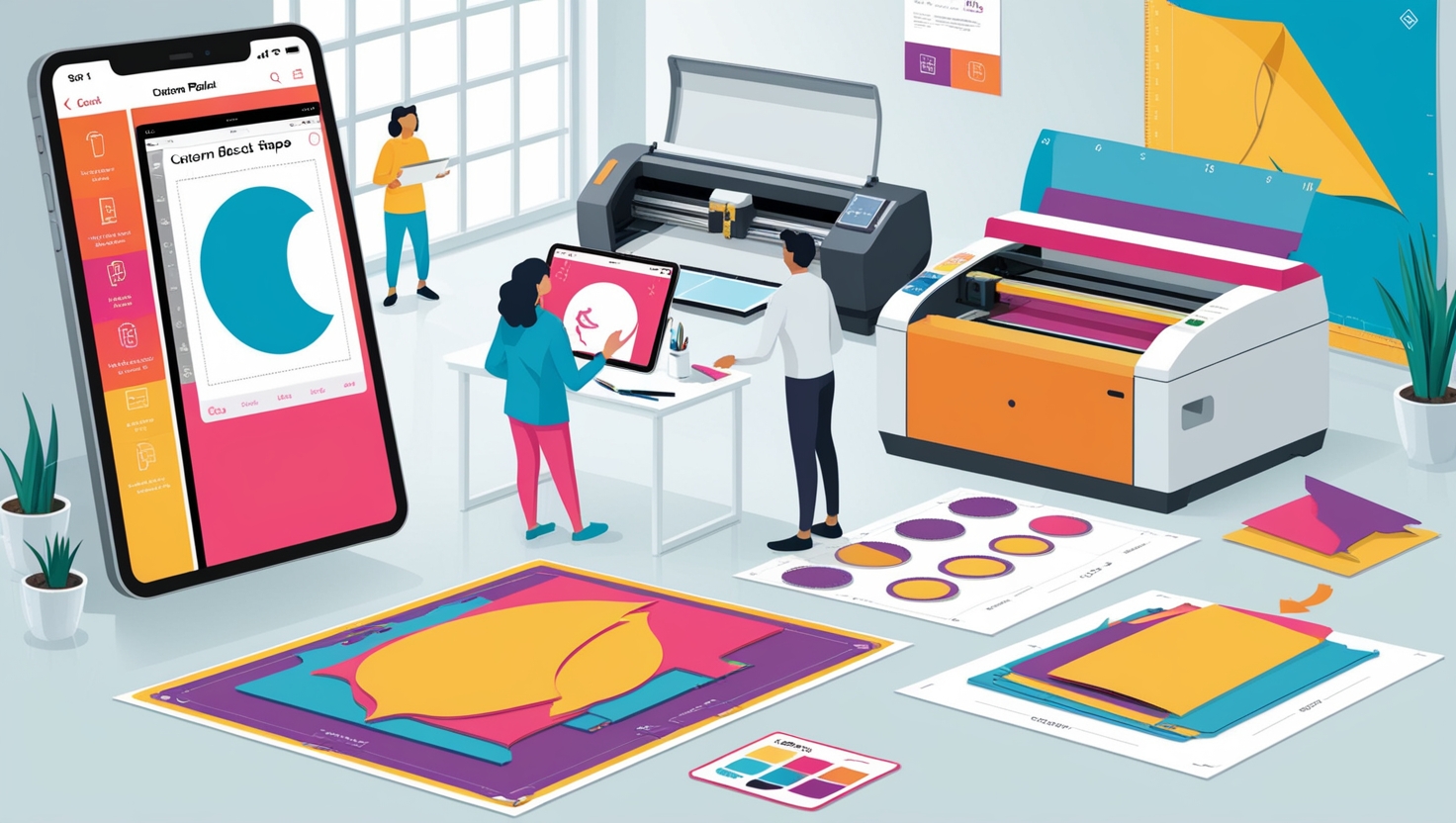
Implementing Spot Colors for Die Lines #
When you design die-cut artwork, using spot colors is key. Spot colors, or Pantone colors, are special inks for your design. They help make sure important parts, like die lines, look right and stay the same.
Choosing Appropriate Spot Colors #
To make your die lines pop, pick a bright color for them. Magenta or a bold blue works great. This makes the die lines easy to see. For fold lines, pick a different color to show them apart from cut lines.
Setting Up Color Swatches #
In your design software, like Adobe Illustrator, make a new color swatch. Name it “die cut” or “dieline.” Choose “Spot Color” and pick your color. Use this color for all die lines to keep things consistent.
For designs with fold lines, make another color swatch. Use it for those lines. Good color management is vital for die-cut projects. Label all spot colors clearly and use them the same way to avoid mistakes.
“Spot colors are the key to achieving precision and clarity in die-cut designs. By effectively incorporating them into your workflow, you can elevate the overall impact of your packaging or marketing materials.”
Preparing Artwork for Production at namecards.com.sg #
When getting your artwork ready for production at namecards.com.sg, make sure all important parts are inside the safe zone. This zone is usually 1/8″ from the die-cut line. This step helps avoid losing key details during the cutting process.
Also, convert all text to outlines or include all fonts used. This keeps your design looking just right.
To make things easier, include all linked images or send them with your artwork. This way, namecards.com.sg won’t have to search for missing files. Also, remove all color profiles to ensure your design looks the same on any device.
Lastly, check that your die lines are set to the right spot color and that all artwork goes to the bleed area. By following namecards.com.sg’s file submission and formatting guidelines, you’ll get top-notch die-cut name cards. These will show off your brand’s professionalism and care for detail.